Our client
Rapid Action Packaging (RAP) designs and manufactures packaging for the food and retail industry, providing solutions for high street names such as McDonald’s, KFC, Pret a Manger and Starbucks to name a few. With a head office in Wimbledon and a state of the art 24/7 manufacturing facility in Ireland there is a great deal of reliance on IT to keep their business working efficiently.
The Client’s Challenge
Backup and Disaster Recovery (BuDR) is an ongoing challenge and for Rapid Action Packaging it was broken down into the following areas:
- Increasing data storage on the servers was creating technical problems with the external hard drive backups, and this, coupled with the potential for the data growth to exceed the growth of external drive capacities was an ongoing worry.
- Using external hard drives and rotating them on a daily basis completely relies on a member of staff and this can lead to missed backups.
- A standard problem with any backup is that if the server hardware becomes completely unusable through a disaster (fire, theft, flood plus fundamental hardware failure) so before being able to restore your system you would need to purchase some new hardware.
- Based on our calculations we worked out that even with the backup solution they had, the best case scenario to have the servers back up and running as they were before the disaster, would be 3 days (probably more).
- Given the reliance that the factory in Ireland has on the servers in the UK office, it was decided that in the event of a disaster, three days of down-time, was not financially acceptable.
Our proposal
Our proposal was divided into two elements:
- Provide an off-site copy of the head office server backups which was fully automated and requires no staff input, which can be monitored 24/7 to make sure it is fully operational.
- Purchase a new high end server that can be setup so that it is pre-configured and ready to load the off-site copies of the backups, reducing the time to deliver a replacement fully functional server.
How we implemented our proposal
Off-site backup: we purchased a large Network Attached Storage (NAS) drive, once configured we took this onsite and replicated the customer’s main backups. We then installed the drive at our office, allowing for overnight replications, only transferring the information that had changed since the last backup – providing a complete mirror image.
We purchased and built a high-end server. Once the off-site backup replication was in place; with the capacity to run all of their head office servers, using virtual server technology. We then configured the backup images and pre-loaded them onto the spare server – saving us time (if required) in the future.
The Result
For the off-site data replication. we have implemented our management and monitoring solution which means that every day we know if there has been any problem with the overnight transfer, which we can then resolve as part of the managed service. Even without the DR server in place, this would guarantee that should their head office burn down we know that their data is safe and the business can be rebuilt.
The key with any Disaster Prevention is to test it and with the server and backup in our office we are able to do this and having carried out the tests we were able to bring up all of the Disaster Recovery copies of the customers servers within 1 hour meaning that they could either log in remotely and carry on working or we could simply deliver their backup server to a location of their choice ready for use directly.
For more information on Disaster Prevention please click here or call us on 020 8649 9911.
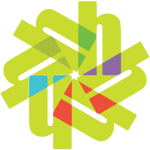